Multifunctional customizable specifications can be configured
Rework station corresponding to the next generation
Meisho Rework Station, MS9000SE has the All-in-one type specification that can easily attach various additional options from BGA, CSP, chip (micro type), desoldering (cleaning function), hot air top heater, IR top heater.
MS9000SE also can be automatable as the rework system.
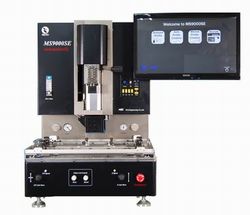
Meisho adopts replaceable attachment structure for various functional options. Thus it enables users not to need to return to the Meisho Fab or remodel it later”, and users can greatly reduce the cost by exchanging the functional option units by the customer only if necessary.
· Cost can be greatly reduced.
· Anyone can operate with same quality.
· Quality assurance is also complete.
Desoldering head
Chip components 01005 –
IR heater
Suitable for various applications
Even if rework and mounting of chip components are unconsidered, no need to purchase new equipments, and what you need is only to buy the low-cost option units.
It is possible to reduce all factors such as 【new equipment cost, transportation cost and time required for delivery】.
From the view of the hardware:
Flatness, squareness, parallelism: Within 20㎛
Z axis repeatability : within 10㎛
Moreover, since it is highly durable and highly accurate, which has been proven numerically, it is safe to move at the time of installation, relocation or moving overseas etc.
Quality assurance is also complete
Fulfilling aftercare service
A fulfilling after-sales service that can be done because Meisho is a manufacturer that produce and develops at Meisho’s own factory.
The system can add more functions and can be modified after installation.
Since it is possible to add functions even after the installation of the equipment, there is no need to consider additional equipment for occurrence of the unexpected rework demand.
⇒ Minimize risk after installation, boost customer’s sales, reduce customer’s leadtimeFrom the view of the hardware:
Flatness, squareness, parallelism: Within 20㎛
Z axis repeatability : within 10㎛
Moreover, since it is highly durable and highly accurate, which has been proven numerically, it is safe to move at the time of installation, relocation or moving overseas etc.
Quality assurance is also complete
Fulfilling aftercare service
A fulfilling after-sales service that can be done because Meisho is a manufacturer that produce and develops at Meisho’s own factory.
The system can add more functions and can be modified after installation.
Since it is possible to add functions even after the installation of the equipment, there is no need to consider additional equipment for occurrence of the unexpected rework demand.
⇒ Minimize risk after installation, boost customer’s sales, reduce customer’s leadtime
Meisho’s rework station has the Auto profile system. It does not require any test samples to obtain the optimal thermal profile data, and it is possible to get the thermal profile data by the only one heating operation with ease.
Meisho’s auto profile system
Repair and other unexpected rework of the PCB can be done without getting any prior thermal profile data as well.
Common auto profile systems
They need to do trial operation for the first time, and also need to take the profile several times after the twice for temperature correction.
Users can reduct working time more than 50% only by Meisho’s auto profile function!
MS9000SE made it possible for anyone to easily obtain the proper thermal profile data based on many user’s voices that the rework operation is one of the “most troublesome / difficult job”.Meisho’s rework station has the Auto profile system. It does not require any test samples to obtain the optimal thermal profile data, and it is possible to get the thermal profile data by the only one heating operation with ease.
Meisho’s auto profile system
Repair and other unexpected rework of the PCB can be done without getting any prior thermal profile data as well.
Common auto profile systems
They need to do trial operation for the first time, and also need to take the profile several times after the twice for temperature correction.
Users can reduct working time more than 50% only by Meisho’s auto profile function!
MS9000SE made it possible for anyone to easily obtain the proper thermal profile data based on many user’s voices that the rework operation is one of the “most troublesome / difficult job”.
Specification | MS9000SE PC | MS9000SE PC LL |
Max. PC board size | 300×400 | 400×500 |
Target device size | □1~□50(0402~Option) | □1~□50(0402~Option) |
Power Supply | Single PhaseAC200V~240V | Single PhaseAC200V~240V |
Top Heater | 1040W | 1040W |
Main Bottom Heater | 1000W | 1000W |
Wide Bottom Heater | – | 2000W |
Thermal sensor connectivity | K Type 1~6ch | K Type 1~6ch |
Thermal Profile Method | AP-mode/M-mode | AP-mode/M-mode |
Equipment Dimension | 1050(W)×700(D)×950(H)mm | 1450(W)×850(D)×950(H)mm |